Oszczędny młyn
Instalacje Vertimill należą do standardowych rozwiązań domielania drobnoziarnistych surowców. Okazuje się, że w przeciwieństwie do młynów kulowych są one efektywniejsze, również przy grubszym uziarnieniu nadawy do 6 mm. Ogólne koszty eksploatacyjne zakładu w instalacjach z Vertimill są o 35% niższe niż przy tradycyjnych młynach kulowych. Każdy oszczędzony megawat w przemiałowni na pierwszych i wtórnych stadiach rozdrabniania prowadzi do oszczędności gotówkowych ok. 10 mln $ i 80 000 ton CO2 w przeciągu 10-letniej eksploatacji jednej kopalni.
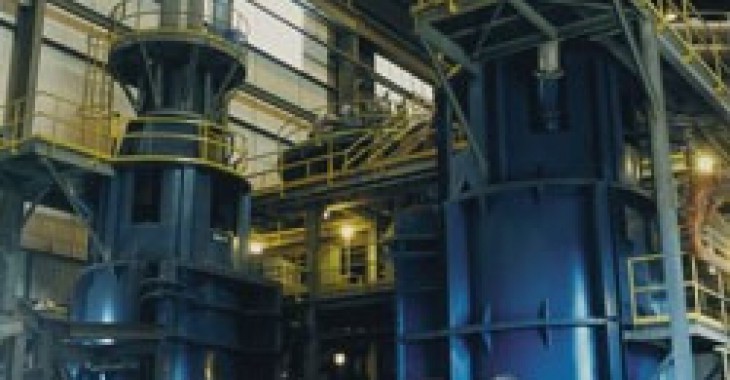
Rozwój technologii mielenia surowców drobnoziarnistych w młynach pionowych kulowych
Młyny pionowe należą do grupy młynów z komorą roboczą nieruchomą i z mielnikami przemieszczającymi się swobodnie, którym energia rozdrabniania przekazywana może być przez wirnik trzpieniowy, gładki lub ślimakowy. Technologia przemiału w młynach pionowych z wirnikiem ślimakowym typu Vertimill została zapoczątkowana w latach 50. ubiegłego wieku w Japonii w przeróbce surowców mineralnych. Wprawdzie w tym okresie nie stawiano wysokich wymagań dla przeróbki surowców, toteż młyn nie był uznany za wystarczająco dobry. W 1979 roku fi rma Metso Grinding nabywając licencję, położyła olbrzymi nacisk na rozwój młynów w tej dziedzinie. Przedsiębiorstwo to na przestrzeni wielu lat modernizowało maszyny pod kątem wzrastających efektów mielenia, minimalizacji okresów remontowych i jednoczesnego wydłużenia żywotności elementów roboczych. W tym okresie światowa technologia najczęściej korzystała z rozwijającej się nowoczesnej technologii wertykalnego domielania surowców drobnoziarnistych, a obecnie liczba instalacji technologicznych z Vertimill wzrasta i jest coraz bardziej opłacalna [1,2]. Obecnie młyny pionowe Vertimill stosowane są w przemyśle górniczym, cementowo-wapienniczym oraz energetycznym. Najczęściej są wykorzystywane do przemiału surowców mineralnych twardych, średnio twardych i miękkich, a także do wytwarzania paliw energetycznych zawiesinowych na bazie drobno zmielonego i zmieszanego węgla oraz oleju lub wody, czy również do mielenia i gaszenia wapna.
Charakterystyka młyna pionowego Vertimill
Instalacja Vertimill, która dostępna jest w standardowej wielkości 20-3000 KM (15-2240 kW) umożliwia duże możliwości zastosowania w zakładzie przeróbczym. Młyn zdolny jest przerabiać nadawę o wielkości uziarnienia poniżej 6 mm do drobnoziarnistego produktu od 74 μm do 2 μm (rys. 1). [3]. Wydajność danej instalacji zależy od zapotrzebowanego przerobu i praktycznie młyny te pracują z przerobem ponad 500 Mg/h. Pod względem mechanicznym młyny pionowe Vertimill są urządzeniami prostymi. W komorze mielącej zawieszony jest na łożyskach baryłkowych przenośnik spiralny. Napęd przenoszony jest od silnika ze stałą prędkością obrotową i pośrednio przełączany mechanizmem planetarnym. Wewnętrzna część konstrukcji młyna jest chroniona przed zużyciem przez okładziny. Ślimak, który również jest narażony na działanie ścierające, jest wyposażony w specjalne metalowe okładziny. W normalnych warunkach pracy te części maszyny wymagają wymiany w odstępach od sześciu do dwunastu miesięcy. Mielniki (kule stalowe, ceramiczne lub naturalne otoczaki do 30 mm) poruszają się po ślimaku. Wodę i nadawę doprowadza się przez otwór w górnej części młyna. Zewnętrzna pompa powoduje wzrastanie prędkości poruszania się cząstek, przez co dochodzi do wstępnej klasyfi kacji cząstek w górnej części młyna. Klasyfi kacja i usunięcie z nadawy ziaren drobnych redukuje przemielenie i powoduje wzrost wydajności. Drobne cząstki są usuwane, a większe opadają i z zawiesiną są kierowane do mielenia. Mielenie następuje poprzez ścieranie. W trakcie rozwoju konstrukcji młynów Vertimill rozmiary ich były nieustannie powiększane. Pierwszy młyn w branży górniczej dysponował mocą zaledwie 450 KM (335 kW), obecne młyny osiągają moc do 3000 KM (2240 kW). Dla bardzo dużych instalacji przeróbczych są potrzebne większe młyny. Ponadto młyny pionowe mają znacznie prostszą konstrukcję od dużych młynów kulowych, a zatem wymagają mniejszej konserwacji. Również młyny pionowe mają wystarczającą żywotność, lepsze bezpieczeństwo i wysoką elastyczność. Konstrukcja młyna Vertimill ogranicza jedynie możliwości zastosowania w przemiałach grubouziarnionej nadawy. Grube ziarna materiału wymagają wcześniejszego przekruszenia do wymaganej wielkości uziarnienia. Typowy Vertimill może mielić twarde surowce mineralne o wielkości nadawy D95 równej 6 mm. Metso kontynuuje badania nad możliwościami poszerzenia zastosowania młynów, przy jednocześnie możliwym obniżaniu energii w szerokim zakresie mielenia. Dla wcześniejszych konserwatywnych porównań szacuje się, że Vertimill w stosunku do młyna bębnowego kulowego przy gruboziarnistej nadawie i uzyskiwanym produkcie (d80<200 μm) jest efektywniejszy o ok. 30%, a przy drobniejszym uziarnieniu nadawy i uzyskiwanym produkcie (d80<200 μm) o ok. 35%.
Korzyści wynikające z zastosowania technologii przemiału surowców w młynie Vertimill w odniesieniu do młynów bębnowych kulowych
Młyny pionowe w porównaniu z klasycznymi młynami kulowymi przy przemiale surowców w zależności od ich właściwości fizyko-mechanicznych zużywają od 30 do 50% mniej energii. Im drobniejsza jest nadawa, tym instalacja z młynem pionowym daje większe oszczędności energetyczne w stosunku do młyna kulowego. Podwyższone korzyści energetyczne uzyskuje się dzięki mieleniu w młynach Vertimill ze względu na pionowe usytuowanie komory. Przedstawiając w uproszczeniu, w młynach grawitacyjnych bębnowych kulowych wzajemnie ścierają się mielniki i surowiec, przy czym nadawa w następstwie staje się łamana i zmielona. Rozdrabnianie bazuje z jednej strony na ścieraniu oraz na udarze, który w zakresie drobnego przemiału nie jest wydajny. Przy ruchu wodospadowym mielników większość energii udarowej zanika. Dzieje się to, gdy mielniki napotykają się z innymi mielnikami albo okładzinami. Najefektywniejsza strefa mielenia wewnątrz walczaka jest znana z kształtu „nerki”, jaką przybiera podczas ruchu. Jej zwiększona efektywność zawdzięcza nieustannemu kontaktowi mielników z ziarnami surowca podczas ścierania [4]. Wewnątrz młyna Vertimill przebieg całego mielenia utrzymywany jest w takiej samej wysokiej sprawności, jak podczas ścierania w obszarze „nerki” występującej w młynie bębnowym kulowym. Spirala obraca się wolno, tak żeby wsad materiału z mielnikami nie uzyskiwał za dużej rotacji. Materiał z mielnikami wyciągany jest do środka młyna spiralą, aż w końcu przez jej krawędź przepływa dalej w dół wzdłuż obwodu młyna. Prędkości cząstek są bardzo nieznaczne, ponieważ mielniki pozostają ze sobą w kontakcie, podczas gdy mielniki w młynie bębnowym mogą się przemieszczać dowolnie w otwartej przestrzeniu bębna. Pionowe ukształtowanie komory młyna zmniejsza wewnętrzną klasyfikację cząstek materiału, toteż nie dopuszcza do przemielenia i w efekcie podwyższa znacznie efektywność procesu mielenia. Nadawa mielona wchodzi do obszaru górnej części komory młyna i przepływa przez wylot młyna, a następnie przez klasyfikator w dół z powrotem do komory młyna. Poprzez obieg materiału z części strumienia zawiesiny w klasyfikatorze przelewowym oddzielane są drobne cząstki materiału, które nie są z powrotem zawracane do młyna. System zewnętrznej klasyfi kacji młyna niewielkim nakładem energetycznym zapobiega przemieleniu się materiału. Kolejną podstawą wzrostu wydajności mielenia w młynie Vertimill jest efektywniejsze wykorzystanie drobniejszych mielników. Zasadą mielenia w młynie bębnowym kulowym jest przynajmniej częściowe rozdrabnianie za pomocą udaru, dlatego wymagany jest określony rozmiar kul, taki aby trajektoria ich rzutu spowodowała wystarczającą energię kinetyczną. W młynie pionowym, przeciwnie większe rozmiary kul nie są wymagane, ponieważ przebieg mielenia nie polega na udarze, lecz na ścieraniu. Do tego można młyn nieznacznie przepełnić mielnikami, co wyraźnie prowadzi do poprawy rozdrabniania ze względu na wzrost powierzchni mielników [1]. Ogólnie powierzchnia mielników w typowym młynie pionowym jest ponad 3-krotnie większa od powierzchni odpowiadającej wsadowi kul w młynie bębnowym. Tabela 1 obrazuje, jaki duży wpływ może mieć mała zmiana rozmiaru mielnika na powierzchnię mielników. Najwięcej zainstalowanych młynów Vertimill do rozdrabniania rudy miedzi pracuje w Chile i w większości są one stosowane do procesu domielania. Na świecie w 85% przypadków drobnego domielania są stosowane młyny tego typu. W pewnym zakładzie przeróbki rudy miedzi w Chile [2] można było porównać oba typy młynów, które były stosowane do drobnego przemiału. Młyn pionowy osiągnął przy tym samym stopniu zmielenia o 44% mniejsze zużycie energii. Oba młyny były wypełnione kulami o rozmiarze 26 mm. Natomiast przy załadowaniu młyna Vertimill cylpebsami <12 mm, energetyczne oszczędności przekroczyły 50% przy identycznych warunkach.
Cały materiał do przeczytania w magazynie "Surowce i Maszyny Budowlane" 6/2014