Lepiej zapobiegać niż… płacić
Biorąc pod uwagę relacje kosztów wdrożenia systemu diagnozowania maszyn i kosztów związanych z niekontrolowaną awarią, udział monitorowania i diagnostyki jako narzędzi wspomagających zarządzanie eksploatacją maszyn odgrywa ogromne znaczenie i może przynieść duże oszczędności.
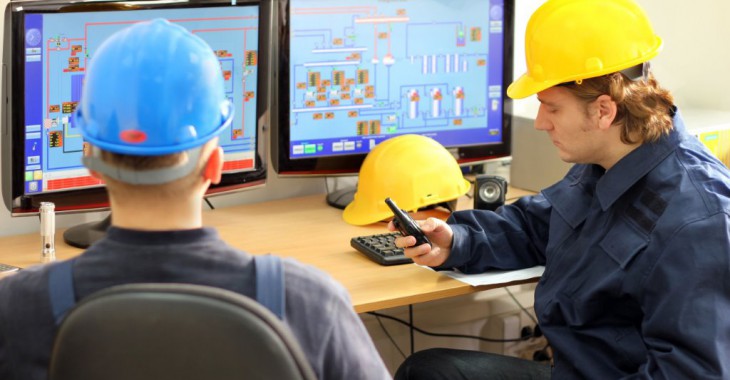
W zakładach przemysłowych związanych ze strategicznymi sektorami gospodarki lub w zakładach produkcyjnych, w których ze względu na technologie nawet nieznaczne niekontrolowane zmiany wybranych parametrów procesu produkcyjnego mogą okazać się krytyczne, znaczenie monitorowania (ciągłego lub okresowego) oraz diagnostyki stanu technicznego obiektu odgrywa znaczącą rolę. Biorąc pod uwagę relacje kosztów wdrożenia systemu diagnozowania maszyn i kosztów związanych z niekontrolowaną awarią (naprawy lub zakup nowych elementów, wymiana maszyn, transport, przestój ciągu technologicznego itd.), udział monitorowania i diagnostyki jako narzędzi wspomagających zarządzanie eksploatacją maszyn będzie coraz większy. Inwestycje lokowane w systemy nadzorowania i diagnostyki maszyn powinny być poprzedzone gruntowną analizą: ekonomiczną, prawną, ekologiczną, społeczną, bezpieczeństwa itp.
Przegląd metod diagnozowania w Polsce
Obecnie w Polsce istnieje kilka firm zajmujących się produkcją, sprzedażą sprzętu do diagnostyki, a także świadczeniem usług diagnostycznych. Większość z nich dostarcza narzędzia do monitorowania lub oprogramowanie – zestaw estymat i analiz, które wymagają eksperckiej wiedzy do prawidłowej interpretacji [13,18,19,21]. Biorąc pod uwagę specyfi kę sektora górniczego, nie wszystkie rozwiązania stosowane np. w sektorze petrochemicznym mogą być przeniesione w prosty sposób do polskich kopalń. Intensywne badania w zakresie diagnostyki prowadzone są w kilku ośrodkach naukowych w Polsce, między innymi w Zakładzie Systemów Maszynowych Instytutu Górnictwa Politechniki Wrocławskiej [2,23]. Z różnych publikacji wynika, że w ocenie stanu technicznego maszyn standardem staje się tzw. diagnostyka zorientowana uszkodzeniowo, czyli precyzyjne zidentyfi kowanie rodzaju niesprawności [15]. Takie podejście pozwala na oszacowanie stopnia zagrożenia związanego z wystąpieniem awarii oraz planowanie remontów (przygotowanie odpowiednich maszyn, podzespołów i specjalistów). Jeżeli zależy nam na wykrywaniu konkretnego rodzaju uszkodzenia występującego pojedynczo, np. dla przekładni: wyłamania zęba, pittingu, bicia wału, uszkodzenia łożyska znane są w literaturze analizy diagnostyczne, które umożliwiają ich wykrycie. W praktyce takie sytuacje występują stosunkowo rzadko, co oznacza, że zastosowanie jednej metody może nie wystarczyć do pełnej oceny stanu technicznego obiektu [4,8,10,11,12,23]. Szczegółowe informacje na temat możliwości diagnostyki, metod przetwarzania sygnałów diagnostycznych i diagnozowania przekładni zębatych można znaleźć w pracach [2-12], [15], [23]. Badania prowadzone w ośrodkach akademickich pokazują, że proste śledzenie pewnych symptomów np. wartości średnich, skutecznych, maksymalnych sygnałów czy podstawowe analizy diagnostyczne, np. widmo, nie dają jednoznacznej oceny stanu technicznego [6,9,15,23]. Wiąże się to np. z niskoamplitudowym charakterem pewnych uszkodzeń, które dopiero we zaawansowanym stadium powodują wyraźny wzrost ogólnego poziomu drgań. Biorąc pod uwagę wzajemne oddziaływanie elementów obiektu, tak jak to ma miejsce np. w wielostopniowej przekładni zębatej, wykrycie uszkodzenia w zaawansowanym stadium oznacza przyspieszone zużycie także pozostałych elementów i dodatkowe koszty. Wydawałoby się, że dobrym rozwiązaniem jest zatem monitorowanie ciągłe stanu technicznego połączone z diagnostyką obiektu. Do podjęcia decyzji o monitorowaniu niezbędna jest charakterystyka niezawodnościowa obiektu. W zdecydowanej większości przypadków awaria poprzedzona jest zużyciem, które można wykryć we wczesnym stadium rozwoju, stosując metody diagnostyczne podczas okresowych kontroli stanu. Monitorowanie opłaca się w przypadku maszyn o nieznanej charakterystyce (nie jesteśmy w stanie oszacować czasu awarii), bądź kiedy chcemy maksymalizować czas prac maszyny (wyłączyć tuż przed awarią). Zachodzi więc znów konieczność analizy potrzeb – jakie maszyny wymagają monitorowania ciągłego, jakie okresowego, jak często niezbędne są kontrole itd. Prawidłowe zdefi niowanie potrzeb pozwala określić środki, jakie należy przedsięwziąć, aby te potrzeby zaspokoić. Do rozważenia jest nie tylko aspekt czysto techniczny problemu (tj. jaki sprzęt, jakie sygnały, jakie analizy, monitorować czy sprawdzać okresowo itp.). Istotne są także sygnalizowane powyżej problemy natury ekologicznej: szybka reakcja we wczesnych stadiach nieprawidłowej pracy i wymiana uszkodzonych podzespołów, a zwłaszcza regulacją, np. ustawienie silnika względem przekładni skutkuje zwiększeniem trwałości systemu, (duża trwałość powoduje że powstaje mniej zdegradowanych obiektów – czyli de facto odpadów), mniejsze zużycie energii (zgodnie z teorią maszyny jako procesora energii zużycie jest skutkiem kumulacji energii strat w danym elemencie maszyny), mniejszy poziom hałasu itp. Poza tym szybka reakcja w początkowej fazie niesprawności daje szansę na minimalizację nakładów związanych z naprawą maszyn czy „reusingiem” jej elementów. Pojawia się także zagadnienie zasobów ludzkich – niski poziom wymagań diagnostycznych oznacza proste urządzenia i co za tym idzie niewielkie nakłady na szkolenia personelu. Niestety, diagnostyka na niskim poziomie przyniesie niewielkie zyski. Zaawansowane metody diagnostyki – jak już wspomniano powyżej – pozwalają wykrywać konkretne formy niesprawności, lokalizować uszkodzenia, znane są także rozwiązania umożliwiające przewidywanie terminu najbliższej awarii – wymagają jednak znacznych nakładów fi nansowych na sprzęt oraz na szkolenia pracowników w zakresie obsługi i interpretacji uzyskanych wyników. Wszystkie te rozważania prowadzą nieuchronnie do zagadnienia analizy opłacalności stosowania diagnostyki rozumianej jako ocena zysków i strat będących, jak każda inwestycja, funkcją wielu czynników (ekonomicznych, technicznych, prawnych, ekologicz
nych, społecznych, bezpieczeństwa itp.). Konieczne jest więc znalezienie odpowiedzi na najważniejsze pytanie: ile i w jaki rodzaj diagnostyki zainwestować, aby można było na tym zaoszczędzić?
Cały materiał dostępnny w magazynie Surowce i Maszyny Budowlane 6/2014.
Fot. photogenica