Poprawa efektywności pracy wysokociśnieniowych pras walcowych
Prasy walcowe coraz częściej pojawiają się w przemyśle cementowym, wapienniczym czy przeróbce rud. Warto zwrócić uwagę na problem doboru optymalnych warunków ich pracy. Odpowiednie wykorzystanie pras pozwala na uzyskanie wymaganej jakości produktów rozdrabniania, przy redukcji niepotrzebnych kosztów obsługi urządzenia.
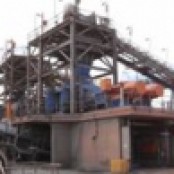
Przemysłowe procesy rozdrabniania są operacjami niezwykle kosztochłonnymi. W USA około 30% całkowitych kosztów energii zużywanej w przemyśle górniczym pochłaniają operacje rozdrabniania surowców (wskaźniki za 2005 r.). Przy takich wskaźnikach energia na rozdrabnianie stanowi mniej więcej 0,39% całkowitej energii zużywanej rocznie w tym kraju. W Kanadzie z kolei, analogiczny wskaźnik wynosi niecałe 2%, podobnie jest w RPA, w Australii rozdrabnianie stanowi około 1,5% całkowitego zużycia energii (Tromans 2008). Warto zauważyć, że wymienione kraje są liderami w rozwoju technologicznym w sektorze górniczym i wartości prezentowanych wskaźników uległy zmniejszeniu w ostatnich latach na skutek zastosowania zaawansowanych technologii przeróbczych oraz nowoczesnych maszyn, w szczególności w układach przygotowania surowca do wzbogacania. W wielu krajach liczących się w branży górniczej na świecie procesy przygotowania rud do wzbogacania bazują na starszych technologiach co powoduje, że procesy rozdrabniania pochłaniają o wiele więcej energii. Można szacować, że przemysłowe procesy rozdrabniania konsumują nawet powyżej 3% światowego zużycia energii elektrycznej.
Prasa walcowa w zakładzie przeróbki rud, Australia (fot. D. Saramak)
Zalety pras walcowych
Biorąc pod uwagę powyższe fakty nie ulega wątpliwości, że zastosowanie wysokociśnieniowych pras walcowych w technologicznych procesach rozdrabniania przynosi szereg korzyści z ekonomicznego punktu widzenia oraz pod względem jakości otrzymywanych produktów (Gawenda 2009, Naziemiec i Saramak 2009). Główne zalety pras walcowych, które należałoby wymienić, są następujące:
• jednostkowe zużycie energii elektrycznej w prasach walcowych według różnych badań jest niższe o 10-40% w porównaniu z młynami (Rule i in. 2008; Fuerstenau i in. 1991);
• niższe są koszty eksploatacji urządzenia i koszty inwestycyjne w porównaniu z tradycyjnymi instalacjami (np. układ typu: kruszarka, przesiewacz-klasyfikator, młyn prętowy, młyn kulowy), a także z młynami samo- i półsamomielącymi, ze względu między innymi na niższą zabudowę instalacji przeróbczej (Morrell 2008);
• występuje selektywne rozdrabnianie w przypadku rud, które ogranicza możliwość przemielania surowca w przypadku grubo wpryśniętych składników użytecznych, które mogłyby się przedostać do odpadów w procesie wzbogacania;
• pojawia się selektywne mielenie surowców węglanowych, co zapobiega przemielaniu w przypadku przemysłu wapienniczo-cementowego;
• występuje zjawisko mikropęknięć, które zwiększa efektywność dalszego rozdrabniania (mielenia) i obniża energochłonność procesu;
• relatywnie wysoki (w zależności od doboru parametrów procesu rozdrabniania) jest udział produktu o uziarnieniu poniżej 0,1 mm, co ma znaczenie przy produkcji mączek;
• powierzchnia zabudowy urządzenia jest stosunkowo niewielka, szczególnie w odniesieniu do wydajności.
Pośród innych zalet należy wspomnieć o możliwości prowadzenia procesu na sucho oraz na mokro. Jednak badania wykazują, że wilgotność materiału nie powinna być zbyt duża, ponieważ powoduje to jego poślizg w komorze roboczej urządzenia, co tym samym obniża wydajność urządzenia. Według niektórych badań nieco zwiększa się zużycie okładzin pras walcowych dla zbyt wilgotnej nadawy. Na podstawie doświadczenia autora w tym zakresie można stwierdzić, że istnieje pewien poziom wilgotności, akceptowalny z punktu widzenia osiąganych efektów technologicznych, a także ekonomicznych. Badania w tym zakresie trwają. Kolejną zaletą jest także łatwość utrzymania stałego przerobu prasy walcowej, co umożliwia płynniejsze prowadzenie procesu rozdrabniania.
Mimo iż technologia rozdrabniania z użyciem wysokociśnieniowych pras walcowych została wyczerpującoopisana z teoretycznego punktu widzenia, w praktyce pewnym problemem jest wytrzymałość okładzin walców, szczególnie przy przerobie bardziej abrazywnych rud metali czy diamentów. Okładziny stanowią od kilkunastu do kilkudziesięciu procent ceny prasy walcowej, a zbyt szybkie ich zużywanie i wynikająca z tego częstsza wymiana znacznie podnoszą koszty eksploatacji urządzenia, obniżając tym samym jego efektywność ekonomiczną. Producenci prowadzą intensywne badania nad poprawą trwałości okładzin osiągając stopniowo coraz dłuższy czas ich żywotności. Zbyt intensywne zużycie okładzin walców związane jest miedzy innymi z nieodpowiednim doborem parametrów roboczych urządzenia, w szczególności zbyt wysokiego ciśnienia roboczego w prasie. W tym aspekcie dodatkowego znaczenia nabiera problem optymalnego doboru parametrów procesu technologicznego do fizykomechanicznych parametrów surowca (podatność na rozdrabnianie). Prasy walcowe są także bardzo podatne na uszkodzenia powierzchni roboczej walców spowodowane zanieczyszczeniem nadawy elementami metalowymi oraz zbyt dużymi kawałkami skał. Aby wyeliminować przedostanie się kawałka metalu do komory roboczej prasy stosuje się kilkustopniowe systemy detekcji oraz usuwania metalowych elementów z nadawy do prasy walcowej. Na samym początku zamontowane są bramki magnetyczne wychwytujące metalowe elementy z materiału. W kolejnym etapie, na taśmociągu dostarczającym materiał do prasy walcowej, umieszczone są bramki wykrywające metal. W przypadku wykrycia elementów metalowych uruchamia się automatyczny system usuwania powodujący samoczynny zrzut partii materiału z taśmociągu, bez potrzeby zatrzymywania procesu. Oprócz bramki wykrywającej metale układ posiada optyczny system detekcji umożliwiający zlokalizowanie elementu o odmiennej barwie, np. kawałków drewna itp. Gdyby jednak metalowy element nie został wychwycony w pierwszym lub drugim etapie, tuż przed prasą walcową umieszczona jest jeszcze jedna bramka detekcji metalu. W przypadku wykrycia niepożądanych elementów uruchamia się alarm powodujący awaryjne zatrzymanie taśmociągu i prasy walcowej, a miejsce wykrycia elementu metalowego oznaczone zostaje przez automatyczny marker rozpylający kolorową farbę w domniemanym obszarze wykrycia zanieczyszczenia. Przedstawiony system funkcjonuje w jednym z australijskich zakładów przeróbki rud złota.
Podsumowując, prasy walcowe są bardzo efektywnymi urządzeniami do rozdrabniania zarówno w przemyśle cementowo-wapienniczym, jak również dla twardszych rud metali i niemetalicznych, a problem zbyt intensywnego zużycia okładzin roboczych można w dużym stopniu ograniczyć poprzez dostosowanie parametrów procesu rozdrabniania do specyfiki przerabianego surowca.
Rys. 1. Instalacje przemysłowe z wysokociśnieniowymi prasami walcowymi na poszczególnych kontynentach
Rynek pras walcowych
Aktualnie wysokociśnieniowe prasy walcowe produkują trzy firmy: KHD Humbolt Wedag, Koeppern i Polysius. Od połowy lat 80. do roku 2000 zostało zainstalowanych w przemyśle cementowym, wapienniczym oraz przeróbki rud żelaza i niemetali ponad 400 pras. Według danych KHD, do połowy 2008 roku w samych procesach rozdrabniania rud zainstalowano 35 pras przy przeróbce diamentów, 42 w rudach żelaza oraz 35 przy wzbogacaniu innych rud. Do połowy lat 90. ubiegłego wieku przemysłowe aplikacje wysokociśnieniowych pras walcowych w przemyśle przeróbczym rud nie były zbyt częstą praktyką, głównie z uwagi na problemy z zapewnieniem odpowiednio długiej żywotności okładzin walców przy pracy z twardszymi skałami; maszyny głównie były kupowane przez przemysł cementowo-wapienniczy.
Struktura aplikacji przemysłowych wysokociśnieniowych pras walcowych dla poszczególnych kontynentów przedstawiona została na rys. 1, natomiast dynamikę wzrostu liczby przemysłowych urządzeń w poszczególnych dekadach obrazuje rys. 2.
Rys. 2. Liczba zainstalowanych pras przemysłowych na świecie w poszczególnych dekadach
Analizując rys. 2. można zauważyć, że dynamika wzrostu zainstalowanych maszyn w przetwórstwie twardszych minerałów jest zdecydowanie większa. Powodowane jest to postępem badań nad zwiększeniem trwałości okładzin, który nastąpił od lat 90. ubiegłego wieku. Mimo wolniejszej dynamiki wzrostu maszyn w przemyśle cementowo-wapienniczym liczba zainstalowanych pras w tych sektorach przewyższa sektor przeróbki rud. Można szacować, że w latach 2001-2009 zostało zainstalowanych 150-200 pras w tej branży.
KHD i Koeppern preferują prasy, w których stosunek wymiarów walców roboczych jest zbliżony do jedności: szerokość robocza walca/średnica walca ≈ 1
Polysius natomiast preferuje prasy, w których podanystosunek jest mniejszy od jedności. Dla pras z mniejszą szerokością roboczą walców możliwe jest zastosowanie prostszych rozwiązań technologicznych związanych z ułożyskowaniem rolek, ale przez to zmniejszona jest wydajność prasy (mniejsza szerokość robocza rolek), w większym stopniu występuje też zjawisko niedokruszania materiału na brzegach rolki (tzw. edge effect). Aby zwiększyć wydajność urządzenia trzeba wtedy produkować maszyny z większą średnicą walców, lub prowadzić proces na ich zwiększonej prędkości obrotowej. Polysius i KHD produkują prasy walcowe z kołkowym (fot. 1a) systemem okładzin (tzw. studs), podczas gdy Koeppern używa okładzin zbudowanych z sześciokątnych elementów (fot. 1b), których struktura przypomina plaster miodu (Hexadur).
Fot. 1. Główne typy okładzin walców w wysokociśnieniowych prasach walcowych: kołkowe (od lewej) oraz plastrowe heksadur (od prawej)
Dobór optymalnych parametrów pracy
Parametrami pracy wysokociśnieniowych pras walcowych, które mogą być bezpośrednio ustawiane przez operatora, są: ciśnienie robocze [bar] (lub przeliczony na jego podstawie nacisk właściwy Fsp) oraz prędkość obrotowa walców (v). Kluczowym parametrem jest ciśnienie robocze, które następująco determinuje główne efekty pracy (przy wzroście wartości ciśnienia):
• zwiększa się stopień rozdrobnienia materiału,
• powstaje więcej mikropęknięć w ziarnach,
• zmniejsza się wydajność urządzenia,
• wzrasta pobór energii elektrycznej prasy,
• następuje zwiększone zużycie okładzin roboczych walców,
• zwiększa się udział i stopień sprasowania aglomeratów (płatków) w produkcie rozdrabniania (co może wpływać na spadek efektywności przesiewania),
• zmniejsza się szerokość szczeliny wylotowej.
Z technologicznego punktu widzenia najważniejsze są: stopień rozdrobnienia produktu oraz jego skład ziarnowy. Pomimo panującego poglądu, głoszonego także przez niektórych producentów, że stosowanie wysokich wartości ciśnienia roboczego jest korzystne z punktu wiedzenia uziarnienia produktów rozdrabniania, osiągane efekty technologiczne (stopnie rozdrobnienia produktów) charakteryzują się relatywnie mniejszymi wartościami dla skrajnie wysokich wartości Fsp. Laboratoryjne testy rozdrabniania w HPGR przeprowadzone przez autora w Norwegii wykazały, że zależność pomiędzy osiągniętym stopniem rozdrobnienia a wartością nacisku w prasie może być opisana za pomocą funkcji potęgowej y1, w której wartość parametru B jest mniejsza od jedności, lub funkcji logarytmicznej y2:
gdzie y1, y2 – funkcja stopnia rozdrobnienia (zmienna zależna); x – wartość ciśnienia operacyjnego w prasie walcowej (zmienna niezależna); A, B, C, D – parametry, które są zależne od cech fizykomechanicznych materiału. Wyniki eksperymentów przedstawia rys. 3.
Rys. 3. Zależność pomiędzy wartością ciśnienia roboczego a S50 oraz S80 dla procesu rozdrabniania rud
Charakter przebiegu dopasowania zależy od podatności na rozdrabnianie surowca, jednak zawsze będzie obserwowane stopniowe wygładzenie przyrostów stopnia rozdrobnienia w miarę zwiększania wartości Fsp. Wiąże się to z cechami materiału i przebiegiem procesu dezintegracji ziaren w komorze roboczej prasy. Jeżeli stopniowo zwiększa się siłę nacisku w prasie, na początku następuje stosunkowo łatwe rozdrabnianie, pęknięcia występują głównie wzdłuż granic ziaren. W miarę zwiększania siły nacisku materiał w komorze roboczej jest coraz bardziej skompresowany i nowe pęknięcia pojawiają się rzadziej.
Wartość ciśnienia roboczego wpływa na wydajność prasy walcowej pośrednio poprzez zmianę szerokości szczeliny wylotowej. Przy wyższych ciśnieniach roboczych następuje mocniejszy docisk rolek do warstwy materiału pomiędzy obracającymi się walcami, a tym samym ulega zmniejszeniu szerokość szczeliny roboczej. Wydajność wysokociśnieniowej prasy walcowej przedstawia poniższy wzór, z którego wynika, że przy zmniejszeniu szerokości szczeliny roboczej (s) wartość przerobu urządzenia (W) ulegnie zmniejszeniu (przy zachowaniu niezmiennych wartości pozostałych parametrów) (Naziemiec i Saramak 2009)
gdzie W – przerób prasy walcowej, s – szerokość szczeliny roboczej, L, szerokość robocza walców, ρ - gęstość sprasowanego produktu rozdrabniania. Pewne korekcje w zakresie zwiększenia wydajności w takim przypadku można uzyskać poprzez zwiększenie prędkości obrotowej walców.
Prędkość obrotowa walców odgrywa mniejsze znaczenie w procesie rozdrabniania w wysokociśnieniowych prasach walcowych. Jej główny wpływ jest związany z wydajnością urządzenia, co zostało wspomniane w poprzednim akapicie. Badania wykazują, że niewielkie zmiany prędkości obrotowej nie mają znaczącego wpływu na zmianę stopnia rozdrobnienia materiału, natomiast wyniki innych badań mówią o efektywniejszym rozdrabnianiu grubszych ziaren nadawy przy wyższej prędkości obrotowej. Można wspomnieć tutaj o nieznacznym obniżeniu energochłonności procesu rozdrabniania wraz ze zwiększeniem prędkości obrotowej, a wynika to z faktu, że zwiększa się przerób, przy minimalnym tylko wzroście poboru energii. Jednak taka poprawa energochłonności procesu nie zawsze jest zauważalna.
Wnioski
Podsumowując, parametrem technologicznym mającym największy bezpośredni wpływ na przebieg oraz wyniki procesu rozdrabniania surowców w wysokociśnieniowych prasach walcowych jest ciśnienie operacyjne. Wraz z jego wzrostem poprawiają się warunki rozdrabniania mierzone zwiększeniem stopni rozdrobnienia produktów oraz powstawaniem większej ilości mikropęknięć. Tym samym obniża się wskaźnik pracy Bonda materiału, zwiększa się powierzchnia właściwa Blaina oraz zachodzi efektywniejsze uwalnianie minerałów użytecznych (w przypadku rud). W przypadku produkcji mączek węglanowych zwiększa się wychód produktu poniżej 0,1 mm. Negatywnym wpływem zwiększonego ciśnienia roboczego jest wyższa energochłonność procesu oraz szybsze zużywanie okładzin roboczych walców, a także nieznaczne obniżenie wydajności. Należy zatem dobrać tak ciśnienie robocze, aby uzyskać optymalne efekty technologiczne przy osiągnięciu zadowalających wskaźników ekonomicznych procesu. Aby tego dokonać należy przede wszystkim wziąć pod uwagę właściwości materiału, co będzie tematem osobnej publikacji.
Literatura
1. Fuerstenau D.W., Shukla A., Kapur P.C.: Energy consumption and product size distribution in choke-fed high-compression roll mills. Intern. Journal of Mineral Processing 32, pp. 59-79, 1991.
2. Gawenda T.: „Główne aspekty rozdrabniania twardych surowców mineralnych w wysokociśnieniowych prasach walcowych", „Górnictwo i Geoinzynieria" rok 33, zeszyt 4, 2009.
3. Morrell S.: A method for predicting the specific energy requirement of comminution circuits and assessing their energy utilization efficiency, Minerals Engineering, vol. 21, issue 3, 2008, pp. 224- 233.
4. Naziemiec Z., Saramak D.: „Analiza zmian obciążenia materiału w strefie zgniotu pras walcowych", „Górnictwo i Geoinżynieria", rok 33, zeszyt 4, 2009.
5. Rule C.M., Minnarr D.M., Sauremann: HPGR – revolution in Platinum?, 3rd Intern. Conference „Platinum in Transformation”, The Southern African Institute of Mining and Metallurgy, 2008.
6. Tromans D.: Mineral comminution: Energy efficiency considerations, Minerals Engineering 21, pp. 613-620, 2008.
Autor: dr inż. Daniel Saramak, Akademia Górniczo-Hutnicza
Artykuł został opublikowany w magazynie "Surowce i Maszyny Budowlane" nr 5/2010