Od wózków do wozideł, czyli z historii wprowadzania transportu samochodowego do procesów wydobywczych w górnictwie skalnym
Jeszcze w latach 50. ubiegłego stulecia załadunek urobku odbywał się ręcznie, na wózki. Obecnie do transportu w kamieniołomie wykorzystuje się wielotonowe wozidła, naszpikowane elektroniką… Prześledźmy tę jakże ciekawą drogę, którą pokonały pojazdy pracujące w polskich kopalniach.
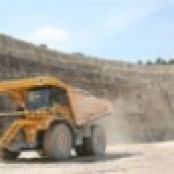
W latach czterdziestych i pięćdziesiątych ubiegłego wieku, w kraju podnoszącym się po zawieruchach wojennych, proces eksploatacji kopalin w kamieniołomach był niezwykle prymitywny – niewiele różniący się od zarania dziejów górnictwa odkrywkowego. Załadunek urobku odbywał się ręcznie na wózki, tak zwane koleby, poruszające się po szynach o szerokości 500 i 600 mm, rozplanowanych po poziomach wyrobisk. Wózki o pojemności od 1,5 m3 do 2 m3 pchane były ręcznie lub ciągnione przez zaprzęgniętego konia. Dopiero pod koniec lat pięćdziesiątych pojawiły się pierwsze lokomotywki spalinowe. W kamieniołomach podległych Centralnemu Zarządowi Kamieniołomów i Klinkierni Drogowych we Wrocławiu w 1952 roku po raz pierwszy do załadunku urobku wykorzystano koparkę łyżkową.
Lata pięćdziesiąte XX w.
Ze względu na powszechnie stosowany w kopalniach odkrywkowych transport szynowy oraz małe pojemności wózków, wprowadzone do urabiania i ładowania koparki łyżkowe przeznaczone były głównie do budowlanych prac ziemnych. Charakteryzowały się niewielką pojemnością łyżek – ok. 1,2 m3, sporadycznie przekraczających pojemność 2,0 m3. Przejęcie parku maszynowego stosowanego w budownictwie przez kamieniołomy, w szczególności koparek łyżkowych i samochodów samowyładowczych, doprowadziło nie tylko do wzrostu wydajności, ale i do przemian strukturalno-organizacyjnych, które stanowiły rewolucję mechanizacyjną w tym sektorze przemysłu. Wprowadzanie mechanicznego ładowania urobku koparkami łyżkowymi wpłynęło na całkowite zastąpienie transportu szynowego przez samochodowy. Początkowo stosowano samochody-wywrotki, nieprzystosowane do warunków pracy w kopalniach odkrywkowych, stopniowo przechodząc na samochodowy transport specjalistyczny, przeznaczony do ładowania koparkami o większych od opisywanych pojemnościach łyżek. Rozwój transportu samochodowego w górnictwie skalnym nie zawsze odbywałsię prawidłowo [1].
![]() |
Fot. 1. Samochód ciężarowy GAY i koparka E-301 |
![]() |
Fot. 2. Samochód ciężarowy Skoda-Liaz 706 MT i koparka E- 25 |
Lata sześćdziesiąte XX w.
Dopiero pod koniec lat sześćdziesiątych na II Krajowym Zjeździe Górnictwa Odkrywkowego, w materiałach o postępie technicznym w mechanizacji transportu urobku w kopalniach odkrywkowych, dostrzeżono konieczność dostosowania transportu samochodowego do warunków eksploatacji w kamieniołomach:
"Pojazdy samochodowe mające własne niezależne napędy i poruszające się po różnego rodzaju drogach, a nawet bezdrożach, w rozmaitych warunkach terenowych i atmosferycznych nadają się do transportu, szczególnie w warunkach improwizacji i robót górniczych, kiedy złoże np. rozrzucone jest w gniazdach albo przykryte nierównomiernej grubości nadkładem lub kiedy przewidywany okres eksploatacji jest stosunkowo krótki.
W budowie nowoczesnych samochodów ciężarowych dla górnictwa odkrywkowego dąży się do polepszenia zwrotności przez skracanie pojazdów, stosowanie napędów na wszystkie osie, przy czym stosuje się w samochodach o ładowności do 30 ton tylko 2 osie, a powyżej tej ładowności 3. Stosuje się również ogumienie pojedyncze niskociśnieniowe. Do obniżenia współczynnika tary dąży się przez budowę skrzyń aluminiowych. Kanadyjskie doświadczenia w tej dziedzinie wykazały, że skrzynia aluminiowa jest trwalsza od stalowej, bardziej wytrzymała na uderzenia, pozwala zwiększyć ładowność samochodu o 15%, wpływa na powiększenie trwałości ogumienia (20 do 50%), wykładzin hamulcowych, zawieszenia itp. Natomiast cena samochodu przy zastosowaniu skrzyń aluminiowych wzrasta zaledwie o 7,6%. Dąży się do powiększenia komfortu jazdy i poprawy sterowności przez doposażenie zespołów sterowniczych: sprzęgła hamulca i układu kierowniczego układami wspomagającymi. Kabinę kierowcy w nowoczesnych samochodachwywrotkach umieszcza się z boku silnika, tak ażeby silnik nie zasłaniał kierowcy widoczności drogi tuż przed przednimi
kołami. Spaliny są wydmuchiwane ponad kabinę kierowcy, a w samochodach specjalnie przystosowanych do ruchu w warunkach zimowych ogrzewane są skrzynie. W Polsce nie produkuje się samochodów przystosowanych do pracy w górnictwie. Maszyny te importujemy z Czechosłowacji i ze Związku Radzieckiego, a częściowo także z Anglii. W takim układzie dysponujemy różnorodnym sprzętem, do którego często brak części zamiennych i fachowej obsługi. Przyszłość przewiduje lepsze perspektywy transportu samochodowego, gdyż w ramach RWPG planowana jest koprodukcja z ZSRR. Polska ma bowiem produkować silniki do samochodów ciężarowych, budowanych w ZSRR [2].
![]() |
Fot. 3. Samochód technologiczny Biełaz 540A |
Konsekwencją podjętych działań było sprowadzanie na początku lat siedemdziesiątych do Polski z ZSRR radzieckich samochodów do przewozu urobku skalnego, typu: BIEŁAZ 540A, MAZ 503A i KRAZ 256B. Pomimo technicznych wad i nie najlepszych wyników ekonomicznych, samochody te i tak przyczyniły się do znacznego podniesienia wydajności transportu. Wprowadzenie do wyrobisk samochodów o dużej pojemności skrzyni było konsekwentnym rezultatem zapotrzebowania przemysłu skalnego na bardziej elastyczny środek transportu oraz warunkiem koniecznym przy mechanizacji robót załadunkowych i transportowych.
Lata siedemdziesiąte XX w.
Konieczność racjonalnej i ekonomicznej eksploatacji złóż wymuszała usprawnienia i zoptymalizowany dobór maszyn pracujących w układach technologicznych kopani odkrywkowej. Na początku lat 70. w Poltegorze Lasko S.[3] podjął się próby kompleksowego opracowania problematyki transportu samochodowego, a w tym szczególnie optymalizacji układu KSKr (Koparka-Samochód-Kruszarka). Celem badań było między innymi określenie parametrów pracy samochodów w zależności od warunków górniczo-organizacyjnych, sposobu załadunku i wyładunku, warunków jazdy oraz kwalifikacji obsługi. Analizę oparł na materiale empirycznym uzyskanym z obserwacji i pomiarów chronometrażowych przeprowadzonych w 22 kopalniach odkrywkowych surowców skalnych, podległych Zjednoczeniu Kamieniołomów Drogowych. Zjednoczeniu Przemysłu Kamienia Budowlanego. Do badań wybrano kamieniołomy, w których użytkowano niemalże cały asortyment typów pojazdów stosowanych ówcześnie w górnictwie skalnym, w skład których wchodziły samochody o ładowności od 6 do 27 ton. Na wybór kopalń miała także wpływ długość tras dojazdowych, które wynosiły od 47 do 1750 m (w większości przypadków 200-400 m) oraz rodzaje nawierzchni.
![]() |
Fot. 4. Samochód ciężarowy Kraz 256B |
Rezultatem pomiarów i obliczeń była dokładna charakterystyka cyklu jazdy w różnych warunkach technologicznych oraz przy różnych systemach organizacji pracy w kopalni. Na podstawie badań wykazano możliwości poprawy wskaźników technicznych, węzłów technologicznych oraz określono przedziały, w jakich powinny się mieścić ujęte badaniami wskaźniki. Zastosowaną analizą statystyczną materiału empirycznego autor objął poszczególne elementy cyklu pracy samochodów i koparek. Rozważania syntetyczne całego cyklu pracy układu przeprowadzono na tle analiz jego elementów:
• załadunku urobku,
• jazdy z ładunkiem i bez ładunku,
• wyładunku,
• manewrowania pod koparką i kruszarką.
Ponadto w celu scharakteryzowania pracy układu oraz wyznaczenia jego wskaźników technicznych przeanalizowano:
• czasy wykonywania czynności,
• rytmiczność pracy,
• rozkłady gęstości prawdopodobieństwa.
Proces transportu technologicznego rozpatrywano z punktu widzenia elementów składających się na cykl pracy T układu KSKr:
T = tł + tjł + tmkr + tw + tjp + tmk + tt
gdzie:
tł – czas załadunku,
tjł – czas jazdy z ładunkiem,
tmkr – czas manewru przy kruszarni,
tw – czas wyładunku,
tjp – czas jazdy powrotnej,
tmk – czas manewru przy koparce,
tk – czas postojów z przyczyn usterek technicznych.
Proces załadunku częściowo opisano w innej pracy [4]. W tym przypadku zwrócono uwagę na element jazdy, od którego w znacznym stopniu zależy praca całego układu wydobywczego kopalni. Należy w tym miejscu przypomnieć, że stosowano w kopalniach odkrywkowych koparki łyżkowe przeznaczone głównie dla budownictwa (KU-1206, KU-1207). Znacznie później wprowadzono koparki o pojemności łyżki 3,5 m3 (czeskie Škoda E-25, E-302 i E-303) [1]. Prowadzone przeto w latach 70. analizy dotyczyły ładowania na samochody urobku koparkami o małych pojemnościach łyżek.
![]() |
Tab.1. Średnie czasy załadunku samochodów koparkami łyżkowymi |
Poniżej przedstawiono wyniki z badań czasów załadunku urobku koparką KU-1205 na samochody Dutra, Tatra 138, Tatra 180, Kraz 256B i Biełaz 540A oraz koparką E-301 na samochody Tatra 138 i Tatra 180. W wyniku przeprowadzonych analiz określono średnie liczby łyżek potrzebnych do załadunku odpowiedniego typu samochodu (tab. 1). Wyznaczono również średnie czasy załadunku 1 tony urobku, a otrzymane liczby wyraźnie wskazywały, że najlepszym wyborem odnośnie środków odstawy do koparek były wówczas samochody typu Dutra o ładowności 6 t dla koparki KU-1205, oraz typu Tatra 138 o ładowności 12 ton dla koparki E-301 [4].
Na podstawie przeprowadzonej analizy można było już wtedy wyciągnąć wniosek, że efekty ładowania będą tym lepsze, im mniejsza będzie konieczna ilość łyżek do napełnienia skrzyni ładunkowej, jednakże nie mniej niż 2-3 łyżek na jeden pojazd.
W następnej części – lata 70., 80., 90. oraz analizy doboru wozidła dla kopalni odkrywkowej.
Autor: prof. zw. dr hab. inż. Artur Bęben, mgr inż. Przemysław Bodziony, AGH Kraków
Artykuł został opublikowany w magazynie "Surowce i Maszyny Budowlane" nr 1/2011