Technologia rozdrabniania w młynach prętowych
dr inż. Daniel Saramak
AGH w Krakowie
Eksperci w branży przeróbczej coraz częściej ogłaszają schyłek technologii rozdrabniania w młynach prętowych. Argumentują to głównie ograniczonymi możliwościami przerobowymi urządzeń oraz wysokimi kosztami pracy w porównaniu do nowszych technologii rozdrabniania. Czy mają rację?
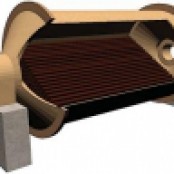
Podobne głosy można usłyszeć przy okazji różnorodnych branżowych konferencji i sympozjów przeróbczych na świecie. Za każdym razem wzbudzają one żywą dyskusję zarówno podczas tych spotkań, jak i na forach internetowych. Zwolennikami ograniczenia zastosowań młynów prętowych w technologicznych układach rozdrabniania na rzecz nowszych rozwiązań, jak chociażby: młyny samomielące (AG), półsamomielące (SAG), prasy walcowe (HPGR) czy młyny pionowe, są zwłaszcza ludzie związani z przeróbką rud. Liczne przykłady pokazują, że dokonane modernizacje układów technologicznych rozdrabniania rud pozwoliły na zmniejszenie zużycia energii i poprawę efektywności pracy zakładu. Z drugiej jednak strony, w roku 2002 Northam Platinum – czwarte największe afrykańskie przedsiębiorstwo wydobywające rocznie prawie 10 ton platynowców, w tym średnio 2,7 tony palladu – zdecydowało się na zainstalowanie nowych młynów prętowych. Młyny prętowe spotyka się także przy produkcji fosforanów (np. Esfordi Phosphates w Iranie). W zakładzie przeróbczym El Teniente, należącym do Chilijskiego koncernu Codelco, wciąż pracuje ponad 20 młynów prętowych 2,4 x 3,7 m, o polskim przemyśle miedziowym nie wspominając. Należałoby się przyjrzeć bliżej tej technologii.
Autor: dr inż. Daniel Saramak, AGH w Krakowie
źródło fot.: zasoby własne autora
Cały materiał znajdą Państwo w magazynie "Surowce i Maszyny Budowlane" 2/2013 zamów prenumeratę w wersji elektronicznej lub drukowanej |