Młyny XXL, czyli co oznacza technologia SAG
Operacje mielenia w młynach przemysłowych są ostatnimi procesami pomniejszania nadawy w technologicznych układach rozdrabniania surowców mineralnych. Występują w wielu gałęziach przemysłu górniczego, od wzbogacania rud metali podstawowych i szlachetnych, po przemiał klinkieru cementowego czy produkcję mączek wapiennych, i pełnią kluczową rolę w prawidłowym funkcjonowaniu zakładu przeróbczego.
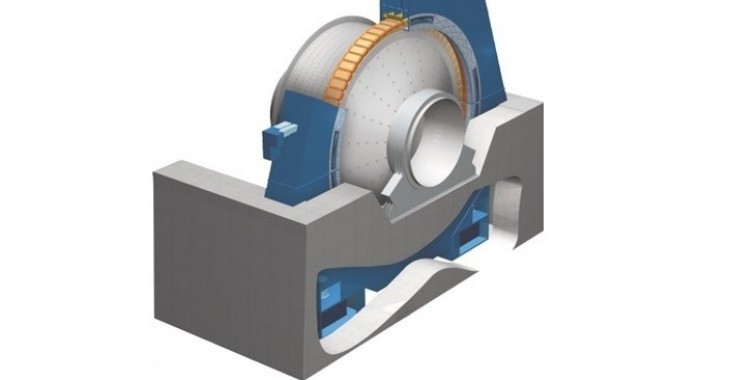
Ze względu na to, że operacje mielenia w młynach przemysłowych są ostatnią operacją redukcji wielkości ziarna materiału, odpowiednie uziarnienie końcowego produktu mielenia jest niezwykle istotne z kilku powodów, zwłaszcza w procesach wzbogacania rud. Optymalne uziarnienie nadawy do flotacji charakteryzuje się właściwym stopniem uwolnienia minerałów użytecznych zawartych w rudzie, przez co zwiększa się odzysk minerałów użytecznych i redukuje się straty. Niedomielenie materiału skutkuje zbyt niskim poziomem uwolnienia minerałów użytecznych, przez co uzyski flotacyjne się obniżają. Przy przemieleniu natomiast proces może stać się mniej opłacalny ekonomicznie ze względu na większe zużycie energii na przemiał oraz straty technologiczne. Inne czynniki związane z koniecznością uzyskania właściwego uziarnienia końcowego produktu mielenia wynikają z oczekiwań klienta lub wymagań kolejnych operacji w technologicznym układzie przeróbczym. Granica pomiędzy kruszeniem a mieleniem, ze względu na rozmiar nadawy, nie jest sztywno określona. Można ponadto spotkać terminy określające bardziej precyzyjnie daną operację rozdrabniania, np. kruszenie grube, kruszenie drobne, mielenie grube, mielenie drobne, które mogą opisywać rozdrabnianie tego samego materiału (np. kruszenie drobne/mielenie grube). Oczywistym jest, że nie określa się procesu mielenia nawet grubej nadawy w młynie prętowym jako kruszenie, zatem typ urządzenia rozdrabniającego jednoznacznie definiuje rodzaj operacji (kruszarka – kruszenie, młyn – mielenie). Niemniej jednak, jeśli chodzi o wielkość ziarna, z mieleniem możemy mieć do czynienia przy rozdrabnianiu nadawy o uziarnieniu poniżej 50 mm. Końcowy produkt posiada uziarnienie w granicach 0,015 mm. Poniżej tej granicy mówimy o mieleniu ultradrobnym.
Specyfika młynów SAG
Młyny samomielące lub autogeniczne (ang. Autogenous, AG), lub półsamomielące albo semi-autogeniczne (ang. Semi-Autogenous, SAG), są typowymi młynami bębnowymi, jednak o znacznie większej średnicy niż młyny prętowe czy kulowe. Dzięki temu materiał jest wynoszony na odpowiednio dużą wysokość wewnątrz komory roboczej, tak że podczas rozdrabniania kluczową rolę odgrywają siły udaru. Rozdrabnianie w młynach SAG jest wspomagane przez dodatek stalowych mielników, które stanowią od 6 do 12% objętości. Młyny SAG mogą być z powodzeniem stosowane przy mieleniu szerokiej gamy surowców, szczególnie dla grubego mielenia, jako przygotowanie nadawy do kolejnych stadiów mielenia w młynie kulowym. Powstanie młynów typu SAG wiąże się z aplikacjami przemysłowymi młynów autogenicznych (AG) w latach 40. i 50. ubiegłego wieku, oraz późniejszym ich rozwojem. W latach 70. zauważono, że uzupełnienie wsadu nadawy w młynie autogenicznym dodatkową porcją mielników poprawia efektywność rozdrabniania. Od tego czasu notuje się dynamiczny rozwój technologii SAG mierzony instalacjami przemysłowymi na całym świecie. Ze względu na fakt, że moce instalowanych młynów SAG stale się zwiększają, częściej podaje się zestawienia aplikacji przemysłowych mierzonych mocą zainstalowanych urządzeń. Szacuje się przykładowo, że do 2000 roku na całym świecie zainstalowano młyny SAG/AG o łącznej mocy około 2,5 mln MW, przy czym moce pojedynczych urządzeń wahały się od 0,25 do 20 MW. Rys. 1 przedstawia procentowy udział młynów SAG w przemyśle przeróbczym ze względu na typ przerabianego materiału. W bieżącym stuleciu nastąpił wzrost przemysłowych aplikacji SAG przede wszystkim w przeróbce rud miedzi i złota. Młyny SAG mogą być wprowadzane w ruch obrotowy za pomocą zębatki zainstalowanej na jednym z końców urządzenia, z jednej lub obu stron młyna. Jednakże w większych urządzeniach występują o wiele większe naprężenia przy kontakcie mechanicznym pomiędzy reduktorami i przekładniami oraz dochodzą problemy z serwisowaniem. W związku z tym opracowano bezprzekładniowy system napędu młyna (rys. 2), w którym elementy wirnika silnika zamocowane są do obudowy młyna, a nieruchomy stojan silnika zainstalowany jest wokół elementów wirnika. Obudowa młyna jest więc niejako obrotowym elementem wielkiego synchronicznego silnika, której prędkość obrotową można regulować poprzez zmianę częstości prądu zasilającego silnik, w zależności od potrzeb technologicznych. Bezprzekładniowe systemy napędowe są efektywniejsze dla większych młynów, z reguły o mocach znamionowych powyżej 10 MW. Pierwsza przemysłowa instalacja samego napędu bezprzekładniowego została zrealizowana przez firmę ABB w 1969 roku. Została w niego wyposażona jednostka mieląca o mocy 6,4 MW i średnicy 16’ zainstalowana w przemyśle cementowym we Francji, notabene wciąż pracująca. Pierwsza instalacja bezprzekładniowego młyna SAG w przeróbce rud miała miejsce w 1986 w Chile i dotyczyła młyna o wymiarach 32’ x 17’ oraz stopnia rozdrobnienia porównywalnego przy zastosowaniu alternatywnego dwu lub nawet trzystopniowego układu rozdrabniania i klasyfikacji, składającego się z reguły z kruszarki bądź młyna prętowego oraz młyna kulowego. Korzyści z takiego rozwiązania są następujące:
• mniejsze jednostkowe zużycie energii elektrycznej w młynie SAG. Według różnych źródeł można uzyskać oszczędności nawet do 15-20% w zależności od typu materiału;
• uproszczenie układu technologicznego i dodatkowe oszczędności z tym związane, a także łatwiejsza obsługa i konserwacja układu;
• porównywalne lub nawet niższe koszty inwestycji w porównaniu do kilkustopniowego alternatywnego układu rozdrabniania;
• możliwość doboru prędkości obrotowej młyna w zależności od potrzeb technologicznych (dla układów napędowych bezprzekładniowych). Zwiększa to efektywność pracy młyna, a także pozwala na budowanie jednostek o w zasadzie dowolnie dużej mocy. Dodatkowo należy uwzględnić fakt, że w zasadzie wszystkie aktualnie konstruowane duże młyny SAG posiadają bezprzekładniowy napęd;
• rozdrabnianie twardszych surowców przebiega w sposób bardziej efektywny, porównując z konwencjonalnymi młynami bębnowymi. Jednostkowe koszty zużycia mielników w młynach SAG są również niższe dla tego typu materiału.
Wśród producentów młynów SAG największe znaczenie mają: Metso, FLSmidth oraz Outotec. Nie jest łatwo podać jednoznaczne dane dotyczące liczby aplikacji przemysłowych każdego z wymienionych producentów, między innymi też ze względu na to, że często operuje się łączną mocą zainstalowanych młynów, a nie ich liczbą. podobny