W kierunku kopalni przyszłości
Wymogiem przyszłości jest zastąpienie górników, w ich najbardziej niebezpiecznych i męczących pracach w kopalniach odkrywkowych i podziemnych, maszynami o sztucznej inteligencji. Powinny to być maszyny górnicze słyszące, widzące i odczuwające, a więc samokierujące i samosterujące, z minimalną interwencją człowieka.
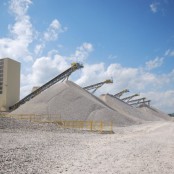
Bezwzględna potrzeba zwiększenia bezpieczeństwa, dyspozycyjności i efektywności pracy maszyn oraz urządzeń górniczych stosowanych w rozległych powierzchniowo, złożonych i kosztownych systemach wydobywczo-transportowych kopalń odkrywkowych wymaga zdalnego sterowania maszynami lub wręcz autonomiczności ich pracy. Dotyczy to szczególnie tych rejonów świata, w których występują trudności w zaangażowaniu fachowców do pracy w kopalni odkrywkowej z uwagi na jej usytuowanie z dala od siedzib ludzkich i w klimacie nieprzyjaznym dla człowieka.
W przypadku górniczych maszyn ścianowych pracujących w podziemiach kopalń węgla kamiennego i innych surowców mineralnych – w warunkach potencjalnych wybuchów, obwałów skał, wysokiej temperatury, intensywnego pyłu, słabej widoczności, wzmożonego hałasu i drgań – istnieje konieczność wycofania załogi z obszarów zagrożonych, co wymaga pełnej autonomiczności działania mechanizacyjnego wyposażenia ściany węglowej.
W ubiegłym wieku próby pełnej automatyzacji ścian węglowych podejmowano w Wielkiej Brytanii – były one określane symbolami ROLF I i II. W Polsce testy takie prowadzono w kopalni JAN, z użyciem sterującej maszyny cyfrowej Master 301 [2]. Nie zakończyły się one sukcesem z uwagi na trudne warunki górniczo-geologiczne i stosowanie elektroniki lampowej o bardzo dużej awaryjności.
Problematyka kopalni przyszłości zostanie przedstawiona na przykładzie kopalń odkrywkowych, które są bardziej zaawansowane we wprowadzaniu kompleksowej automatyzacji, przekształcającej się stopniowo w autonomiczną pracę maszyn górniczych.
Etapy dochodzenia do odkrywkowej kopalni bezzałogowej – łączność
Jednym z najważniejszych czynników zautomatyzowanej kopalni odkrywkowej jest duża prędkość i precyzja wzajemnej komunikacji. Dotyczy to zarówno komunikacji wewnątrz maszyny górniczej, pomiędzy maszynami, jak i między dyspozytorem a maszynami. Dzięki osiągnięciom współczesnej techniki kopalnie dysponują rozległymi sieciami światłowodowymi, gdzie przekazywanie informacji odbywa się z prędkością 100 Mb/s lub 1 Gb/s, lub bezprzewodową telefonią komórkową, internetem, różnorodnymi systemami radiowymi połączonymi z systemem GPS o wysokiej dokładności pozycjonowania maszyn w przestrzeni kopalni odkrywkowej, które wykorzystują satelity. Systemy komunikacji bezprzewodowej mogą stosować mobilne stacje przesyłowe zasilane z baterii słonecznych, co ułatwia ich lokalizację w odkrywce.
![]() |
Fot. 1a Urządzenia łączności wykorzystywane w kopalni odkrywkowej: radar do kontroli stateczności skarpy (źródło: Ground Probe, USA); zespół kamer i radaru zabudowany na wywrotce (źródło: Caterpillar, USA); skaner laserowy Maptek I – Site 8800 (źródło: Maptek I - Site 8800). |
Ważną rolę odgrywa radar bliskiego i dalekiego zasięgu, używany m.in. do oceny stateczności skarp w odkrywce. W pojazdach na podwoziu oponowym lub gąsienicowym stosowane są kamery wizyjne na światło dzienne i na podczerwień z procesorami obrazu, które w kombinacji z radarem ułatwiają operatorowi manewrowanie pojazdem.
![]() |
Fot. 1c |
Systemem o dużym znaczeniu technicznym, wykorzystywanym szeroko w kopalniach odkrywkowych, jest Leica Geosystems, którego częścią są skanery laserowe przeznaczone do szybkiego określania trójwymiarowej topografii odkrywki i zachodzących w niej zmian.
![]() |
Fot. 1b |
Elementy systemu automatyzacji, nadzoru i kontroli układów maszyn roboczych
Tworzenie systemu sterowania obiektem technicznym wymaga na początku precyzyjnego zdefi niowania algorytmu sterowania. Istnieje wiele systemów sterowania, jednak często wykorzystywany jest mikroprocesorowy system automatyzacji, np. typu Promos Plus (fot. 2).
System ten jest używany w obszarze automatyzacji, sterowania, łączności, nadzoru i kontroli, w tym blokad poszczególnych elementów obsługiwanego obiektu (np. taśmociągów). W skład systemu wchodzą: centralny programowalny sterownik PLC (Programmable Logic Controllers) z panelem operatorskim (np. graficznym lub dotykowym), mikroprocesorowe sterowniki rejonowe (np. typu Mincos MMC) i lokalne – między nimi, a innymi elementami układu, komunikacja odbywa się z wykorzystaniem magistrali systemowej Feldbus lub w standardzie Profibus. Urządzeniem sterującym może być także komputer IPC w wykonaniu przemysłowym. Sterowniki lokalne są wyposażone w dowolne karty i moduły sensorowe.
![]() |
Fot. 2. Sterowanie z użyciem systemu Promos Plus przenośnika taśmowego z napędem pośrednim typu TT (Źródło: www. Becker-Mining. com). |
Centralny sterownik, współpracujący poprzez magistralę transmisji danych z układami peryferyjnymi wyposażonymi także w mikroprocesory, pozwala na elastyczne dopasowanie (w obszarze programu użytkownika) właściwości układu do obsługiwanego obiektu. Sterowniki lokalne (np. typu BFS) służą do lokalnej obsługi maszyny lub aparatury przypisanej do magistrali systemu Promos, Promos-Plus, Betacontrol itp. Informacje o stanach pracy maszyn są podawane na wyświetlaczu. Sterowniki te mogą być wyposażone w różne jednostki funkcjonalne, w zależności od warunków w miejscu pracy. Napięcie zasilania wynosi od 8,5 do 12 Vdc, a pobór prądu nie przekracza 1,2 A. Prędkość transmisji (w zależności od zaprojektowania) to 76,8 kb/s. Sterowniki współpracują z sensorami o różnym przeznaczeniu (do pomiaru drgań, temperatury, przemieszczeń itp.) i elementami wykonawczymi (fot. 3)
![]() |
Fot. 3. Sensory i elementy wykonawcze |
Informacje z sensorów są przetwarzane zgodnie z algorytmami i w efekcie generuje się rozkazy dla systemu nawigacji i automatyzacji określonych operacji systemów maszynowych. Sterowniki komunikują się ze sterownikami nadrzędnymi poprzez magistralę systemową Feldbus.
Przedstawiony system automatyzacji w specjalnym wykonaniu firmy Becker-Warkop został zrealizowany do sterowania układem przenośników taśmowych w upadowej odstawczo-transportowej kopalni Marcel w 2008 r.
Kierunki tworzenia bezzałogowej kopalni odkrywkowej
Postęp wiedzy i rozwiązań technicznych w dziedzinie elektroniki, komputeryzacji, przesyłu informacji, elektrotechniki, nowych materiałów i budowy maszyn górniczych, doprowadził aktualnie do utworzenia systemów zdalnego kierowania (sterowania) ruchem maszyn w kopalni odkrywkowej (rys. 1).
![]() |
Rys. 1. Automatyzacja kopalń odkrywkowych z przerywanym transportem urobku i kierunki tworzenia bezzałogowej kopalni przyszłości (Źródło: materiały własne autora). |
Kontakt w czasie rzeczywistym z jednostkami mobilnymi odkrywki pozwala kierownictwu poprawiać pracę operatorów, zwiększyć bezpieczeństwo pracy, wykorzystanie maszyn, transport materiałów i monitorowanie produkcji. System przyczynia się do zwiększenia produkcji o kilkanaście procent i pracy charakteryzującej się zerową szkodliwością. Podstawą nowych systemów jest ich spójna integracja z modelem kopalni i optymalizacja efektywności według przypisanego algorytmu.
Kolejnym etapem jest zdalne sterowanie pracą maszyn i urządzeń zainstalowanych w odkrywce. Istotne jest to, że szereg tego typu systemów zawiera elementy ułatwiające ich przekształcenie w systemy autonomiczne i przejście do bezzałogowej kopalni przyszłości.
Zaawansowane systemy zdalnego kierowania ruchem maszyn górniczych w kopalniach odkrywkowych
Przerywany transport urobku
Przykładem jest tutaj nowoczesny system dyspozytorski zastosowany do kierowania ruchem zbioru oponowych sztywnoramowych wozideł technologicznych (wywrotek) oraz koparek i ładowarek, a także spycharek i ciężkich wiertnic obrotowych w rozległym terenowo kamieniołomie złota Newmont w pobliżu Carlin (Nevada, USA) [8].
W tej kopalni, o bardzo zróżnicowanym złożu złota, dzienne wydobycie wynosi około 300 000 t materiału o wahającym się udziale w nim złota, który zmienia się z dnia na dzień. Do kierowania ruchem wszystkich maszyn górniczych wykorzystywana jest najnowsza wersja 3.0 sytemu Caterpillar MineStar Fleet Commander (2009 r.). Systemem objęto 45 wywrotek modeli Cat 793C, Cat 793D, Cat 789s-plus, koparki hydrauliczne Hitachi EX2500 i EX5500 oraz ładowarki oponowe Cat 994F (dane techniczne tych maszyn podano w tab. 1).
![]() |
Tab. 1. Dane techniczne podstawowych maszyn górniczych w kamieniołomie złota Newmont (USA) (Źródło: materiały własne autora). |
Rozległość pracy wywrotek wynosi około 40 km, zatem aby zrealizować założone zadanie wydobywcze każda musi wykonać około 7,5 cykla, co przy średniej prędkości jazdy wywrotki 30 km/h (jazda z załadunkiem plus jazda bez ładunku) daje około 20 h jej pracy na dobę. Zastosowany system kierowania ruchem maszyn górniczych w omawianym kamieniołomie przyczynił się do blisko 15% wzrostu zdolności produkcyjnej kopalni. Na system ten składa się zaawansowany algorytm przydziału zadań poszczególnym maszynom, otwarta architektura (do współpracy z innymi systemami sterowania), szybka prezentacja graficzna stanu zarządzanego systemu w dyspozytorni i ogólnosystemowa jednolita platforma sprzętowa (wyposażone są w nią wszystkie maszyny i dyspozytornia), która uelastycznia zarządzanie parkiem maszyn górniczych, poprawia bezpieczeństwo i w przyszłości ma być podstawą do zastosowania sztucznej inteligencji w maszynach górniczych.
W tym systemie dyspozytor stale śledzi na szerokoekranowych monitorach stan pracy wszystkich maszyn. Do prawidłowego pozycjonowania sprzętu wydobywczotransportowego wykorzystywane są systemy satelitarne – rosyjski Glonass GPS i amerykański Navstar GPS. Szerokie zastosowanie logistyki transportowej wymaga poprawnej łączności dyspozytora z obsługą maszyn, która występuje w postaci szkieletowej sieci Ethernet, bezprzewodowej 200-megabitowej i łączności radiowej o częstotliwości 11 GHz. Każda wywrotka przed wyruszeniem w wyznaczoną drogę, po załadowaniu jest ważona.
![]() |
Fot. 4. Monitor 15” dotykowy, zainstalowany w kabinie wywrotki Caterpillar (źródło: materiały Caterpillar. |
W kabinach wszystkich maszyn górniczych są zainstalowane stypizowane układy hardwarowe i softwarowe, pozwalające na rejestrację, gromadzenie i analizę szeregu sygnałów pochodzących od czujników obrazujących parametry pracy maszyny. Wywrotki wyposażono w zintegrowany system detekcji obiektów. System ten składa się z kombinacji kamer, radaru i sygnałów alarmowych i ma za zadanie wspomaganie operatora w manewrowaniu wywrotką. Jednym z istotnych badanych parametrów, oprócz zużycia paliwa, jest trwałość opon wywrotek (z uwagi na ich wysoką cenę zakupu).
Do oceny trwałości opon niezbędna jest znajomość:stopnia ścierności drogi jazdy, czasu cyklu, długości drogi cyklu, temperatury otoczenia, masy ładunku, masy wywrotki, rozdziału obciążenia na oś przednią i tylną, nacisku opony na podłoże, nachylenia drogi, prędkości średniej i maksymalnej jazdy wywrotki. Uzyskane dane, po obróbce matematycznej, mogą być porównane z zalecanymi przez producenta opon (Michelin lub Bridgestone). Firma Michelin proponuje stosowanie systemu MEMS (Michelin Earthmover Management System) do natychmiastowego zdalnego pomiaru ciśnienia i temperatury opon. W oponach znajdują się elektroniczne wskaźniki, których wskazania odbiera odbiornik umiejscowiony w kabinie operatora; stąd są następnie transmitowane do dyspozytora odkrywki. System MineStar składa się z szeregu modułów, oprócz modułu Fleet Commander. MineStar Production dostarcza stale informacje o wydobyciu pochodzące od maszyn górniczych w celu poprawy efektywności operacji górniczych. MineStar Material Tracking monitoruje rodzaje materiału i jego przesył w określone miejsce odkrywki. MineStar Machine Tracking ma z kolei za zadanie monitorowanie położenia maszyn, analizę rozładunku i zatłoczenia dróg jazdy. Aquila Drill Systems steruje pracą ciężkich wiertnic obrotowych.
Ciągły transport urobku
W krajowych kopalniach odkrywkowych węgla brunatnego od lat stosowany jest nowoczesny, proekologiczny, zelektryzowany i zmechanizowany system wydobycia, transportu i zwałowania, określany skrótem KTZ – dotyczy on węgla brunatnego przeznaczonego do utylizacji w elektrowni oraz nadkładu zwałowanego w określonych miejscach odkrywki.
W pracach [1, 10] przedstawiono zarys aktualnego systemu sterowania i automatyzacji procesów technologicznych KTZ. Na szczeblu centralnym wykorzystywany jest system nadzoru dyspozytorskiego, w skład którego wchodzi system łączności i wizualizacji pracy układów KTZ. Nadzór ten ma strukturę hierarchiczną. Dyspozytornie lokalne są usytuowane w maszynach podstawowych i w określonych miejscach odkrywki. Informacje od przenośników taśmowych do głównej dyspozytorni i odwrotnie dochodzą liniami transmisji przewodowej lub światłowodowej, a od koparek i zwałowarek – systemem transmisji bezprzewodowej, którą jest radiowe łącze telemetryczne, rys. 2.
![]() |
Rys. 2. Bezprzewodowy system transmisji danych typu KTZ z wykorzystaniem radiowego łącza telemetrycznego (źródło: mat. własne). |
Zdalne sterowanie maszyn podstawowych odbywa się z kabiny operatora koparki oraz z kabiny operatora załadunku. Kabiny te są wyposażone w programowalne sterowniki PLC i współpracujący z nimi system wizualizacji (ekrany monitorów 15” z grafiką maszyny i automatyką ruchów manewrowych), system telewizji przemysłowej oraz w bogaty sprzęt hardwarowy i softwarowy.
Ważną rolę w pracy maszyn odgrywają obwody bezpieczeństwa, sygnalizacji, oświetlenia i łączności. Wymienić tutaj można układy ograniczania ruchów zespołów obrotowych maszyny, sygnalizacji ostrzegawczej, układ przeciwpożarowy, pomiaru prędkości wiatru i pochylenia maszyny.
Duże zastosowanie ma zdalna diagnostyka maszyn podstawowych. Dane diagnostyczne są gromadzone w komputerze wyposażonym w odpowiednie oprogramowanie, współpracującym z bazowym sterownikiem PLC. Informacje przesyła się przez komercyjną sieć telefonii komórkowej ERA GSM, z wykorzystaniem modemów przemysłowych.
Daleko zaawansowane jest sterowanie przenośnikami taśmowymi i ich ciągami. Stacje przenośników w ciągach transportowych [9] są połączone ze sobą liniami transmisyjnymi o różnym charakterze dla potrzeb zdalnego sterownia, kontroli parametrów i rodzaju awarii oraz wprowadzania zdalnych blokad wybranych funkcji ciągów przenośnikowych.
Przykładowo do funkcji kontrolno-sterujących zalicza się: sterowanie rozruchem w funkcji czasu lub prędkości, kontrolę poślizgu taśmy, kontrolę sił w taśmie, temperatury napędów, krzywobieżności taśmy na stacji napędowej, oblepienia bębnów napędowych i zwrotnego itp. Informacje pochodzące z czujników są ujawniane na monitorach dyspozytorskich w postaci szeregu plansz. Występujące sygnały alarmowe podlegają analizie specjalistów. Ogranicza to czas napraw i wymian. Ten system sterowania pozwala na bezobsługową pracę ciągów przenośników taśmowych (węglowych i nadkładowych).
Kopalnia odkrywkowa o wysokim stopniu autonomiczności pracy maszyn górniczych
Koncern RIO TINTO w swoich kopalniach odkrywkowych rudy żelaza (region Pilbara w Australii, obejmujący 11 kopalń, wydobycie 220 mln ton na rok) wdraża największy na świecie cywilny projekt robotyki [9]. Dotyczy on wprowadzenia do kopalni wozideł technologicznych z ramą sztywną (wywrotek) i innych maszyn wyposażonych w układy samoprowadzące i samosterujące, z minimalną bezpośrednią interwencją człowieka.
W kopalni West Angelas zastosowano pełne zdalne sterowanie wszystkimi stanami pracy wywrotek, ciężkich wiertnic obrotowych oraz zautomatyzowaną logistyką transportu i innych czynności technologicznych w odkrywce. Wszystkie operacje maszyn są sterowane z centrum operacyjnego (CO) w Perth, oddalonego o 1500 km. Natomiast w kopalni, z ruchomych kabin, operatorzy obserwują i nadzorują pracę maszyn.
![]() |
Fot. 5. Wozidło z ramą sztywną i napędem spalinowo-elektrycznym typu Komatsu 980 E o ładowności 290 t, wyposażone w system o sztucznej inteligencji do kierowania jazdą (źródło: Grad P.S.: Running with robotics. Engineering and Mining Journal, Jan/Feb 2010). |
Sztuczna inteligencja, zainstalowana w wywrotkach Komatsu 930 E (fot. 5) o ładowności 290 t, uczy się geografii kopalni i rysuje mapę w pamięci komputera. Pojazd jest wyposażony w autonomiczny system jazdy i w liczne sensory (radaru i laserowe), wysokiej precyzji GPS, system detekcji przeszkód i w system bezprzewodowej sieci komunikacji. Wywrotka Komatsu 960 E to najnowsza wersja pojazdu z napędem elektrycznym typu AC, napędzana silnikiem SSDA 18V 170 z wykorzystaniem systemu dwustopniowego doładowania powietrza, który rozwija moc 2610 kW, przy bardzo niskim zużyciu paliwa. Silnik ten napędza prądnicę prądu przemiennego. Pojazd porusza się na oponach wielkości 56/80R63.
Samosterujące wywrotki przesyłają informacje pochodzące z własnych czujników do centrum sterowania (OC), które je rejestruje, przetwarza i analizuje, a następnie odsyła instrukcje określające kurs i prędkość jazdy (do 50 km/h). Pozycje wszystkich maszyn górniczych i urządzeń w odkrywce określane są przy wykorzystaniu systemu precyzyjnego GPS. Ładowanie wywrotek jest maszynowe z udziałem operatora, ale planowana jest jego automatyzacja (przez firmę Terex Mining).
Ciężkie wiertnice obrotowe (fot. 6) o dużych osiągach mają konstrukcję wyjątkowo odporną na różnorodne obciążenia, inteligentny system sterowania i są przystosowane do łatwej konserwacji oraz napraw.
![]() |
Fot. 6. Ciężka wiertnica obrotowa Terex Mining wyposażona w system sztucznej inteligencji, przeznaczona do autonomicznej pracy – jazdy i wiercenia (źródło: Grad P.S.: Running with robotics. Engineering and Mining Journal, Jan/Feb 2010). |
W zależności od decyzji operatora mogą pracować w trybie ręcznym autonomicznym lub zdalnie sterowanym (Terex Mining), z dużą dokładnością pozycjonowania (ok. 15 cm) i zwiększoną prędkością wiercenia otworów strzałowych. Duży postęp w ostatnich latach dotyczy autonomicznego systemu wiercenia obrotowego otworów strzałowych. Firma Caterpillar przewiduje wykorzystanie ulepszonego softwaru i hardwaru stosowanego dotychczas w programie sterowania wierceniem, tzw. Caterpillar AQUILA Drill System. Moduł prowadzenia wykorzystuje nawigację satelitarną do precyzyjnego umiejscowienia otworu i wysokości kołnierza, zezwalających na ustalenie poprawnej pozycji wiertła i dokładne wyznaczenie głębokości wiercenia.
Urobek z kopalni rudy żelaza przewozi się pociągami długości 2,5 km (230 wagonów samorozładowczych) na odległość 350 km do portu Cape Lambert. Pełna automatyzacja przewozu jest możliwa, ale ten projekt jest na razie zawieszony z różnych przyczyn.
Zdobyte doświadczenia z autonomicznej pracy maszyn w odkrywce West Angelas po przewidywanych udoskonaleniach zostaną wykorzystane w innych odkrywkach RIO TINTO i sąsiednich firmy BHP Billiton Pilbara.
Warto zapamiętać
Opisane w pracy nowoczesne systemy sterowania maszynami i urządzeniami pracującymi w kopalniach odkrywkowych pozwalają zaliczyć je do maszyn o autonomicznej pracy. Sensory systemu są zaprojektowane do pracy w trudnych warunkach i zawierają układy radaru bliskiego i dalekiego zasięgu, zapobiegające kolizjom oraz radary do śledzenia stateczności skarp odkrywki, pozycjonowania z użyciem systemów satelitarnych GPS, kamery wizyjne systemów diagnostycznych, kamery pracujące w podczerwieni i inne. Informacje z sensorów są przetwarzane zgodnie z algorytmami i służą do generowania odpowiednich rozkazów dla systemu nawigacji i automatyzacji maszyn.
Podstawowym medium transmisyjnym systemów sterowania maszynami w kopalniach odkrywkowych jest infrastruktura światłowodowa umożliwiająca przesyłanie danych z dużą prędkością na znaczne odległości, łączność radiowa i szkieletowa sieć bezprzewodowa Ethernet. Maszyny systemu są nasycone stypizowanymi układami hardwarowymi i softwarowymi o otwartej strukturze komunikacji, co pozwala na przesyłanie danych do centrum sterowania (głównego lub lokalnego).
Przedstawione w artykule przykłady świadczą o tym, że wszystkie światowe duże firmy i grupy kapitałowe pracują nad maszynami górniczymi o pełnej autonomiczności ich pracy.
![]() |
Literatura
1. Alenowicz J., Sobczyński E.: „Sterowanie maszyn podstawowych w kopalniach węgla brunatnego", Monografia. Komtech 2008, Gliwice 2008.
2. Antoniak J., „Przenośniki zgrzebłowe" Wydawn. Śląsk, Katowice 1968.
3. Antoniak J. „System kruszenia i odstawy przenośnikowej w kopalni odkrywkowej surowców zwięzłych", "Surowce i maszyny budowlane" nr 5/2009.
4. Antoniak J., „Kopalnia przyszłości", Transport przemysłowy i maszyny robocze nr 4/2010.
5. Antoniak J., „Transport taśmowy i koncentracja wydobycia podstawą współczesnego modelu polskiej kopalni węgla kamiennego", Monografia.
Wydawn. Pol. Śląskiej, Gliwice 2009.
6. Antoniak J. „Przenośniki taśmowe w górnictwie podziemnym i odkrywkowym", Wydawn. Pol. Śląskiej, Gliwice 2007.
7. Antoniak J. „Kopalnia przyszłości – mine of the future". Opracowanie własne niepublikowane, Instytut Mechanizacji Górnictwa, Pol. Śl., Gliwice maj 2010.
8. Carter R.A. "Fleet dispatch systems accelerate mine productivity". Engineering and Mining Journal, Jan/Feb 2010.
9. Grad P.S. "Running with robotics". Engineering and Mining Journal, Jan/Feb 2010.
10. Rosseger A., Borczyk Z. „Sterowanie i automatyzacja procesów technologicznych w kopalni węgla brunatnego", „Górnictwo odkrywkowe" nr 6, 2005.
Autor: prof. zw. dr hab. inż. Jerzy Antoniak
Artykuł został opublikowany w magazynie "Surowce i Maszyny Budowlane" nr 4/2010